Il massetto in cemento-sabbia è un modo tradizionale e collaudato per livellare i pavimenti, creare una nuova base per piastrelle, laminato, moquette.
Cominciamo a conoscere la tecnologia di organizzazione di un nuovo pavimento in una stanza con le basi.
Il massetto cemento-sabbia è universale e può essere utilizzato su qualsiasi superficie: cemento, pavimento in pietra o pavimento su base in mattoni.
Composizione della miscela
Raramente vengono utilizzati componenti aggiuntivi per preparare la soluzione: sono sufficienti i due menzionati nel nome del metodo. La soluzione standard viene preparata nella seguente proporzione: una parte di cemento M 300 e 2,5-3 parti di sabbia. Il terzo componente richiesto è l'acqua. Per aumentare la densità del massetto cemento-sabbia si consiglia di aggiungere plastificanti alla soluzione.
IMPORTANTE! Se per sistemare il pavimento di un locale ad alta intensità di sollecitazioni meccaniche viene utilizzato un massetto in cemento-sabbia, il massetto viene realizzato con armatura in ferro (massetto armato).
Figura 1 - Proporzioni dei componenti per la preparazione miscela cemento-sabbia e calcestruzzo (soluzioni M 150 e M 200)
Il massetto cemento-sabbia, se seguito scrupolosamente dalla tecnologia, può sopportare pressioni specifiche da carichi puntuali di circa 500 N/cm2, ed è idoneo all'uso in luoghi pubblici e ambienti ad alta intensità di traffico (zone pedonali, automobilistiche).
Massetto cemento-sabbia: consumo di materiale
Quando si effettuano i calcoli prima di acquistare materiali da costruzione, tenere presente che per organizzare un massetto tradizionale di 4 centimetri sono necessari circa 7 sacchi di cemento (saranno sufficienti per una stanza con una superficie di 13 m²).
In base al rapporto 1:3 è necessaria una quantità di sabbia tre volte superiore, ovvero 21 sacchi (attenzione: spesso la sabbia viene venduta solo in sacchi da 50 kg, mentre il cemento viene venduto in sacchi da 25 e 50 kg).
Peso del massetto cemento-sabbia
Prima di creare un grande trambusto a casa o in ufficio, assicurati che il pavimento della stanza possa sostenere il peso del massetto: potrebbe essere meglio scegliere un'opzione più leggera - ad esempio, realizzare un massetto asciutto invece di uno bagnato uno è adatto anche un massetto semisecco con fibra di vetro.
Prendiamo ad esempio strutture in cemento armato nella costruzione monolitica a telaio. Secondo SNiP, questi possono sopportare circa 400 kg/m² come carico permanente e altri 150 kg/m² come carico temporaneo. Un massetto di 5 cm di spessore darà un carico aggiuntivo sul pavimento di 90 kg/m². Non tutti gli edifici sono progettati per superare la capacità portante del solaio di quasi il 25%.
Prima di iniziare i lavori è meglio consultare gli specialisti o, meglio ancora, approvare il piano di ristrutturazione con gli enti locali competenti.
Quando si calcola il peso del massetto, è importante tenere conto del fatto che il concetto stesso di "peso" non può essere considerato unilateralmente: esistono due sottotipi: peso specifico e peso volumetrico, ad es. il peso di un materiale assolutamente denso e il peso del materiale nel suo stato abituale. Quindi, ad esempio, secondo GOST 8736-77 (Sabbia per lavori di costruzione), il peso volumetrico di 1 m3 di sabbia dovrebbe contenere 1.600 kg e peso specifico la sabbia, secondo lo stesso GOST, può oscillare tra 1.550 - 1.700 kg/m3.
Figura 2 - Tipologie di legami in quanto tali e modalità della loro organizzazione
Funzionalità aggiuntive
Quando si scelgono miscele già pronte, è importante tenere conto di un indicatore come la densità della composizione secca. Esistono massetti di cemento-sabbia leggeri e pesanti: quelli leggeri hanno una densità fino a 1.500 kg/me quelli pesanti - da 1.500 kg/me oltre. La forza della composizione stessa, così come l'isolamento acustico e la resistenza al gelo, dipendono dalla densità del massetto.
Il primo gruppo è adatto per appartamenti e uffici tranquilli.
La conduttività termica della composizione dovrebbe essere presa in considerazione anche quando si acquistano materiali per l'organizzazione del massetto. Nella maggior parte dei casi, la malta cemento-sabbia ha un coefficiente di conducibilità termica di 1,2 W/m per K. Questo non è sempre sufficiente per mantenere temperatura confortevole all'interno, quindi se ne consiglia l'uso materiali aggiuntivi per isolamento.
IMPORTANTE! Per organizzare il pavimento zone umide, così come le stanze frequentemente in contatto con ambiente esterno, è applicabile il cosiddetto massetto “galleggiante” (le pareti e il pavimento sono separati dal massetto da una guarnizione speciale), la tecnologia di lavoro con la quale, oltre alla posa dello strato di guarnizione, non è diversa da quella standard .
Installazione di massetto cemento-sabbia
Fase preparatoria
Il massetto può essere posato in qualsiasi ambiente dove la temperatura del basamento non scenda sotto i +5 °C.
Dopo aver ripulito il pavimento dai vecchi rivestimenti e dai detriti di costruzione, segnare il bordo superiore del massetto.
Per fare ciò, utilizzare una livella idraulica e una corda di intercettazione. Alcuni artigiani, per misurazioni accurate, tracciano una linea di controllo ad un'altezza di 1 m sopra l'orizzonte (!), e da essa si abbassano le perpendicolari all'altezza del massetto.
Figura 3 – Disposizione della stanza
Spessore massetto cementizio dal pavimento non deve superare i 5 cm. Allo stesso tempo è poco praticabile anche la posa del massetto a meno di 3 cm.
IMPORTANTE! Per riparare massetti, ma anche piccole crepe del vecchio sottofondo, è possibile utilizzare l'impasto M 100.
Sulla base pulita e preparata viene posato uno strato impermeabilizzante: un film di polietilene con uno spessore di 8 micron con una sovrapposizione (15-20 cm ciascuno), se un pezzo di film non è sufficiente per coprire l'intera superficie del pavimento. Il film dovrebbe estendersi sulle pareti: l'altezza del margine è determinata in base all'altezza del livello finale del massetto - il film dovrebbe essere 5-7 cm più alto di esso.
Figura 4 — Posa dello strato impermeabilizzante
Il massetto viene posato lungo i fari; è possibile utilizzare anche le doghe dei fari o un profilo metallico a soffitto lungo fino a 3 m (60 mm per 27 mm).
I fari sono montati su alabastro con incrementi di 15-20 cm o su una malta di cemento e sabbia preparata nella proporzione: una parte di cemento M 400 su tre parti di sabbia. Come soluzione di fissaggio è possibile utilizzare anche gesso diluito in acqua. miscela di gesso“VOLMA-Layer” (consumo di materiali di questo gruppo - un sacco di materiale per 13 m²).
I fari devono essere posizionati in file parallele con un gradino fino a 2 m (la lunghezza del gradino è determinata dalla lunghezza del regolo; è più conveniente lavorare, soprattutto per un principiante, con un regolo di 1,5 m) . I fari esterni sono posizionati secondo i segni sulle pareti della stanza, mentre i fari intermedi sono posizionati arbitrariamente, rispettando la lunghezza della regola.
È necessario attendere circa 1,5 ore affinché la composizione di fissaggio sui fari si indurisca.
Figura 5 — Controllo del livello dei primi fari prima dell'applicazione del massetto in cemento-sabbia alla base del pavimento
Inizio dei lavori
La base del pavimento è generosamente inumidita con acqua.
Il massetto viene steso a strisce lungo i fari, preparando la soluzione in porzioni.
Il massetto è livellato secondo la regola.
La seconda striscia non viene colata finché non viene completata la prima (direzione del lavoro: dall'angolo più lontano della stanza alla porta d'ingresso).
L'uniformità del massetto viene controllata con un livello.
Una volta ultimato il getto dell'intera pavimentazione è consigliabile la copertura del massetto pellicola di plastica.
Figura 6 - Livellamento della composizione applicata utilizzando la regola
È necessario attendere almeno 12 ore affinché il massetto si indurisca mediamente.
Facciamolo brillare!
Se sulla superficie del massetto compaiono delle irregolarità o per eliminare asperità è possibile utilizzare una spatola metallica e una grattugia in legno.
Devi aspettare almeno altre 12 ore.
IMPORTANTE! Il massetto indurirà completamente in circa 28 giorni.
Figura 7 — Irregolarità della stuccatura
Molti artigiani consigliano inoltre di adescare la superficie del pavimento prima di iniziare i lavori, e alcuni non sono favorevoli a uno strato impermeabilizzante sotto il massetto, dicono, in caso di allagamento la pellicola di plastica bloccherà solo il percorso naturale di drenaggio dell'acqua.
Non sempre la riparazione con un ritardo di 28 giorni è conveniente, quindi prima di realizzare un massetto “bagnato”, considerare un'alternativa, niente meno opzione affidabile: organizzazione di un massetto “a secco” nella stanza - in soli due giorni la superficie del pavimento livellata sarà pronta per un ulteriore utilizzo!
$ Massetto cemento-sabbia: prezzo di emissione
Se per lavori di costruzione Puoi pagare gli artigiani e preoccuparti della questione del massetto solo al momento dell'ordine, ma l'acquisto dei materiali per il massetto è spesso gravato solo dai proprietari di appartamenti e locali in fase di ristrutturazione.
Quando acquisti materiali da costruzione con le tue mani
Dovresti aspettarti i seguenti prezzi:
- primer per pavimenti Ceresit CT 17 (10 l) - da $ 10,1/confezione;
- faro (3 m) - da $ 0,7/pezzo;
- alabastro per fissare i fari (20 kg) - da $ 5,2/bag;
- sabbia fluviale da costruzione (50 kg) - da $ 8,2/bag;
- cemento M 400 (25 kg) - da $ 3/sacco.
Prezzo del lavoro a noleggio
Quando si organizzano massetti fino a 40 mm di spessore :
- a Mosca − 180 rub./m²
- a Kiev - 45 UAH/m².
Le malte cementizie, come il cemento puro, vengono spesso utilizzate per scopi edili. Presenta numerosi vantaggi rispetto ad altri materiali da costruzione. Ecco perché è molto importante comprendere il calcolo della massa richiesta per gettare fondamenta forti e durevoli. L'indicatore di calcolo principale è peso volumetrico o peso specifico del cemento.
Fattori che influenzano i cambiamenti nella densità del cemento:
Peso specifico della miscela cementizia
Nome/marca del cemento/miscela | Peso specifico (kg/m3) |
M100 | 900 |
M150 | 900 |
M200 | 900 |
M300 | 1100 |
M400 | 1100 |
M500 | 1100 |
Miscela sabbia-cemento | 1700 |
Malta cemento-perlite | 1000 - 1400 |
Malta a base di scorie cementizie | 1000 - 1400 |
Il cemento, durante il trasporto, tende ad arricchirsi di aria. In questo caso, subito dopo lo scarico, peso volumetrico del cemento sarà di 1200 kg/m³. Con il tempo il materiale inizierà a compattarsi e la sua densità tornerà alla normalità - circa 1600 - 1500 kg/m³. Ci sono situazioni in cui il cemento è pieno di umidità e diventa troppo denso, raggiungendo il limite di 3100 kg/m³. Il principale fattore che influenza la variabilità della densità è la dimensione dei trucioli di cemento.
Quando si testano i materiali, è molto importante prestare attenzione a questo indicatore. Anche se, sfortunatamente, controllare la densità di una sostanza non è facile. Ma c'è media, a cui devono attenersi i fornitori - 1300 kg/m³.
Mescolando la soluzione è possibile compattarla. Per fare ciò è necessario riempire il contenitore sabbia grossolana(un mezzo per sigillare), quindi aggiungere quello medio e alla fine quello più fine.
Calcolo del peso volumetrico del cemento per lavori di costruzione
Quando si lavora con miscele edili, calcoli errati dei fabbisogni materiali possono influire sulla produttività e sulla qualità del risultato. Peso specifico del cemento, come qualsiasi altra massa materiale da costruzione, è definito come: M/V, dove M è la massa e V è il volume.
Il rapporto risultante tra massa e volume è misurato in - kg/m³. Un buon esempio calcoli degli idrocarburi di marche famose nella tabella sopra.
Come si può vedere dalla tabella, peso specifico del cemento m 500, m 400 e m 300, è pari o superiore a 1100 kg/m³. Nella produzione esiste un sistema per controllare la massa volumetrica di una sostanza. Aiuta a impostare il valore desiderato utilizzando vari tipi additivi (bario).
Per creare qualità e fondamenta solide Per l'eventuale rivestimento del pavimento di finitura è necessario determinare la capacità portante dell'intera struttura.
Il peso del massetto è piuttosto elevato e pertanto esercita molta pressione sulla base della struttura.
Nei casi in cui il lavoro non viene eseguito utilizzando una miscela già pronta acquistata nei negozi di edilizia, ma una composizione preparata in modo indipendente, è necessario effettuare calcoli accurati tenendo conto delle caratteristiche dei materiali utilizzati.
Scelta dei materiali e preparazione della miscela
Il massetto DSP o cemento-sabbia è necessario e silenzioso in modo semplice superfici livellanti. Per crearlo servono sabbia, cemento e acqua. La quantità di ciascun componente dipende dalle loro caratteristiche.
Quindi, ad esempio, se prendi il cemento di grado M150, avrai bisogno di tre volte più sabbia. Se per preparare la miscela viene utilizzato cemento di grado M500, la sabbia viene prelevata in proporzione 1:5.
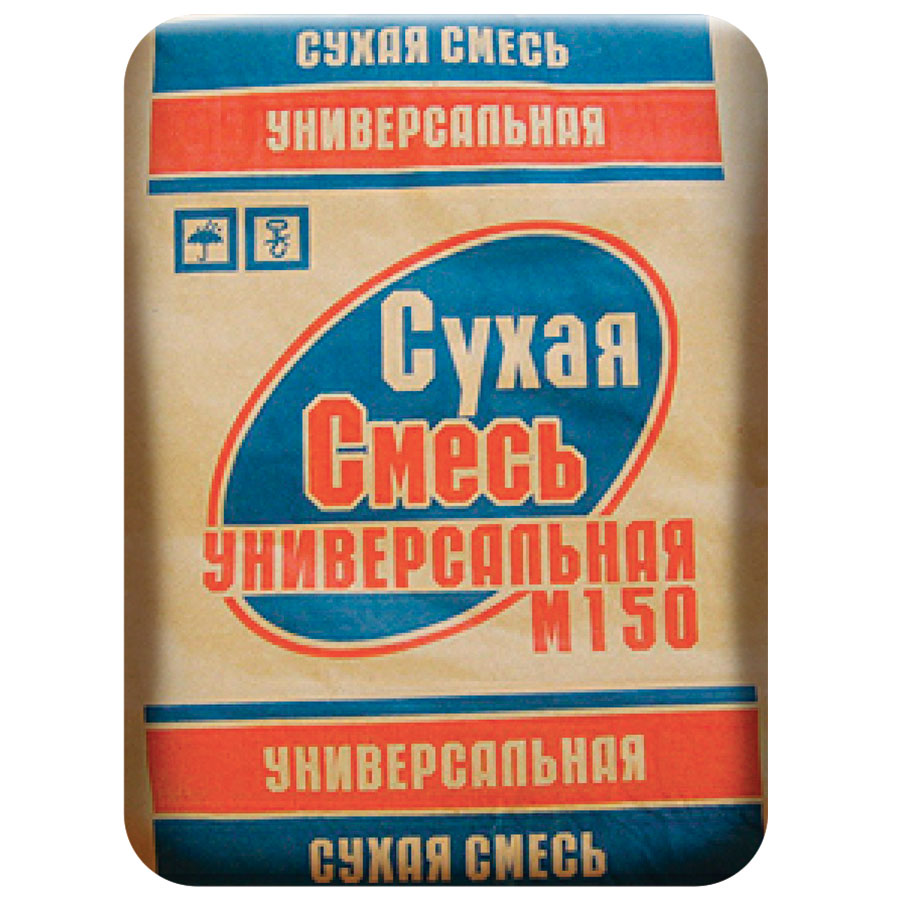
L'uso del cemento di grado M 150 è considerato ottimale, quindi per di questo materiale del peso di 50 kg saranno necessari 150 kg di sabbia. Per quanto riguarda la quantità di acqua, dipende dal contenuto di umidità della sabbia.
Puoi preparare una soluzione di alta qualità prendendo:
- 1 sacco (50 kg) di cemento;
- 15 secchi da dieci litri (150 kg) di sabbia asciutta;
- 27 litri di acqua.
L'aggiunta di sabbia bagnata ridurrà il volume dell'acqua a 25 litri.
Il peso del massetto cemento-sabbia determina la pressione che eserciterà sulla base della struttura. Di conseguenza, prima di iniziare il lavoro, è necessario chiarire lo spessore dello strato versato.
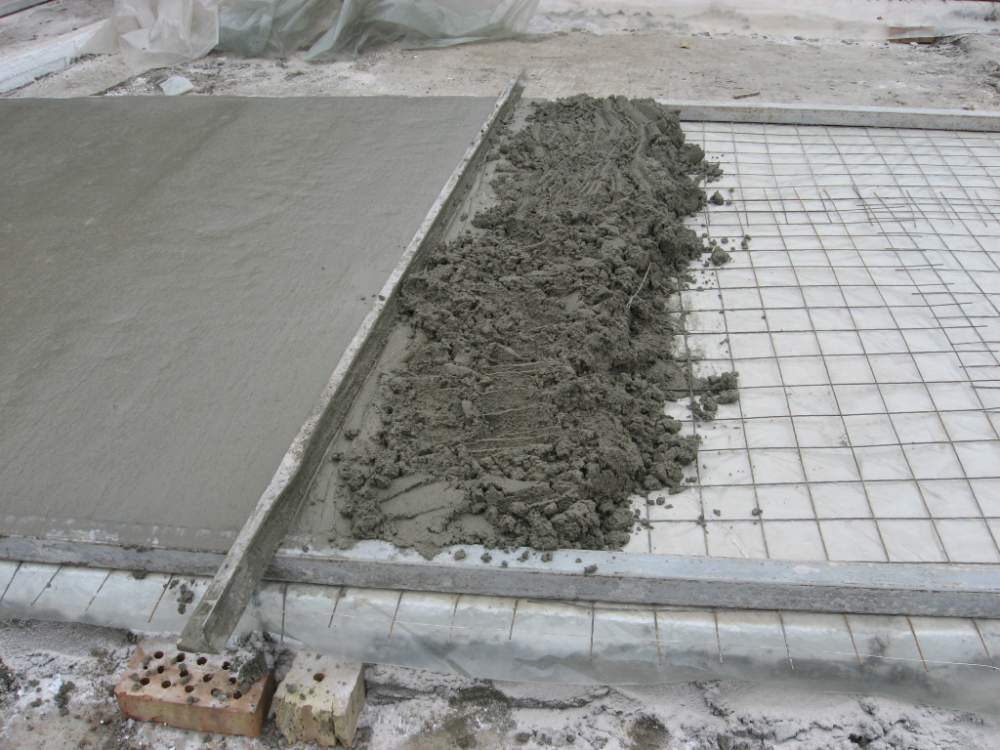
Lo spessore minimo del massetto è di 0,3 cm. Altrimenti, dopo che la soluzione si è indurita, la superficie si ricoprirà di crepe. Il superamento dello spessore massimo di 0,5-1 cm comporta il superamento carico ammissibile sulla base.
Se questo valore raggiunge gli 8-10 cm, il peso del massetto cementizio per ogni metro quadrato sarà di circa 150 kg. Ciò è inaccettabile e pertanto gli esperti raccomandano di non superare i parametri stabiliti.
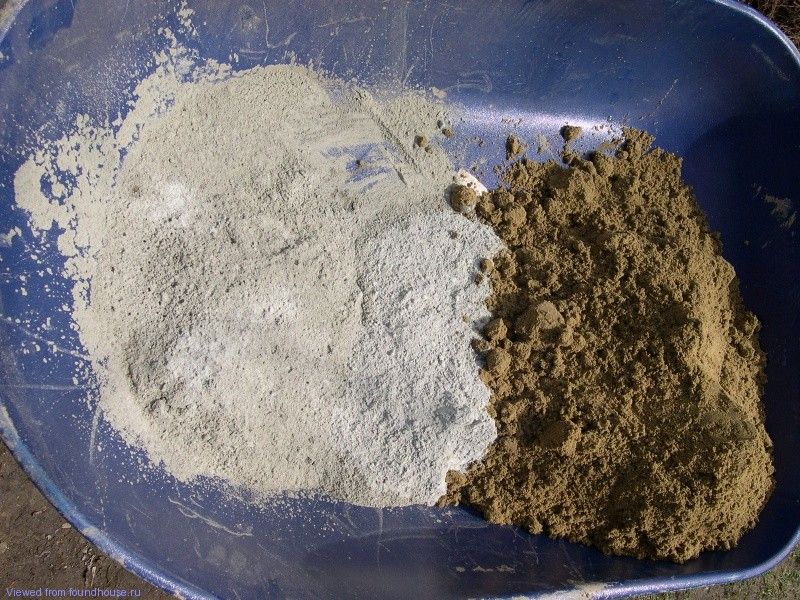
Quando si realizza un massetto cemento-sabbia dello spessore di 1 cm, il suo consumo sarà di almeno 20 kg per metro quadrato. In questo caso, per 1 cm² il suo peso sarà compreso tra 15 e 20 kg.
Quando si crea un massetto di cemento-sabbia, è necessario tenere conto della densità della composizione, che dipende dai materiali scelti dagli artigiani.
In base a questo parametro, le composizioni sono suddivise in:
- Leggero, la cui densità non supera i 1400 kg/m³.
- Cravatte pesanti, indicatore specificato che sono significativamente superiori a 1400 kg/m³.
Se la tecnologia viene seguita rigorosamente, il peso specifico del massetto sabbia-cemento, a seconda delle caratteristiche della sabbia, non supererà i limiti consentiti.
In conformità con GOST 8736-77 uno metro cubo la sabbia non deve contenere più di 1600 kg e il suo peso specifico deve essere compreso tra 1550 e 1700 kg/m³. Per ulteriori informazioni su come realizzare una soluzione, guarda questo video:
È possibile calcolare il consumo di materiali utilizzando la formula esistente e i dati di riferimento. Quando si lavora con grado di cemento M 400 per la realizzazione di un massetto di 3 cm di spessore in un locale la cui superficie è di 50 m², avrete bisogno della seguente quantità di cemento e sabbia, che un semplice calcolo vi aiuterà a scoprire:
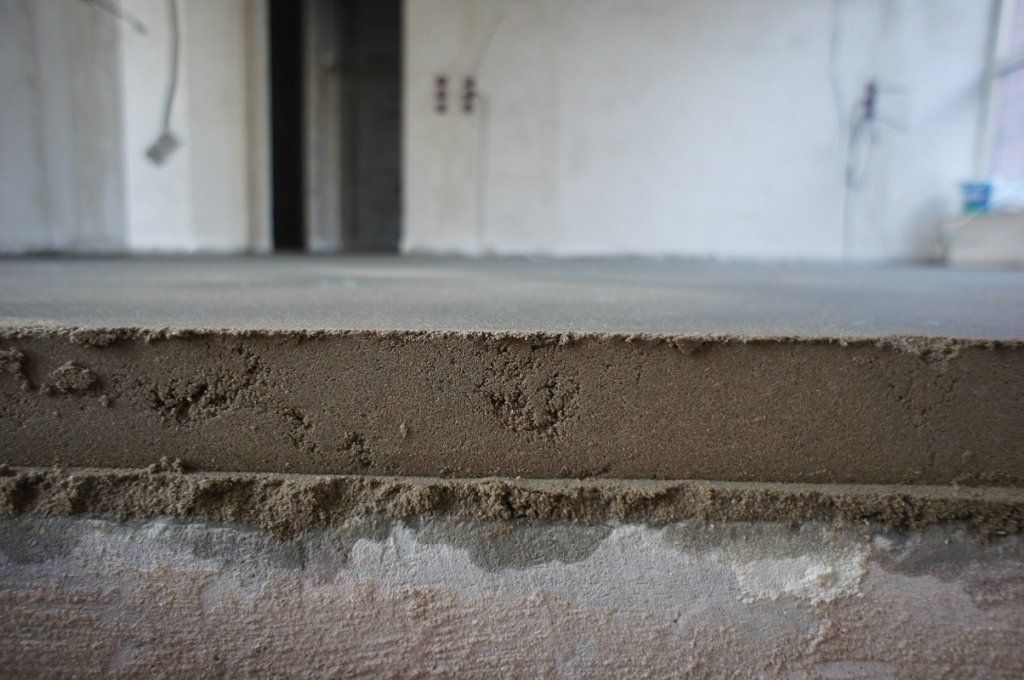
Il volume dell'acqua è determinato in ragione di 0,5 litri per 1 kg di cemento. Saranno quindi necessari 4875 × 0,5 = 2437,5 litri.
Il rispetto di tutti questi standard consentirà di eseguire il lavoro in modo efficiente e di creare una base forte e affidabile per il rivestimento di finitura.
Ordine di lavoro
Le azioni devono iniziare preparando le fondamenta.
Per fare ciò, i pavimenti vengono puliti dai precedenti pavimentazione, liberare la stanza dai detriti di costruzione e posizionare i fari di costruzione, dopo aver determinato l'orizzonte con una livella.
La posa del massetto sabbia-cemento è possibile in qualsiasi locale dove la temperatura della base non scenda sotto i +5 ͦ Celsius.
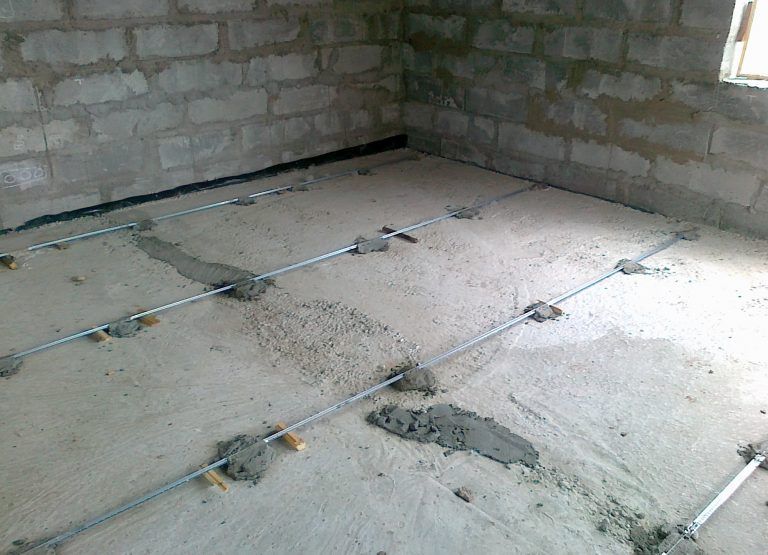
I segnalatori vengono installati su uno strato impermeabilizzante pre-posato, che può essere utilizzato come pellicola di polietilene. I bordi della tela sono posizionati sul muro in modo che sporgano a livello del massetto.
Iniziano a versare il massetto fin dall'inizio luoghi difficili da raggiungere stanza, ma se ha una porta, è importante assicurarsi che la porta non sia bloccata.
Dopo che la soluzione su cui sono installati i fari si è indurita, la miscela preparata viene versata sulla base, riempiendo con essa una striscia. Usando la regola, la soluzione viene livellata e solo dopo che la prima striscia è pronta, iniziano a versare la soluzione nella seconda. Dopo 12 ore, i fari vengono rimossi e lo spazio risultante viene riempito con una soluzione, che impiegherà circa 15 ore per indurirsi completamente.
Ora prepara la miscela di malta ed esegui le manipolazioni associate alla stuccatura della superficie. Avrai bisogno di asciutto o miscela bagnata, costituito da parti uguali di sabbia e cemento. Levigare la superficie utilizzando apposite attrezzature oppure manualmente utilizzando monospazzola o grattugia. Per tutti i dettagli del processo di colata di cemento sui fari, guarda questo video:
Dopo aver completato tutto il lavoro, otterrete una superficie liscia, leggermente ruvida, che dovrà essere stesa con un rullo umido e ricoperta con pellicola trasparente. Inumidire il massetto per almeno sette giorni, trascorsi i quali verrà rimossa la pellicola.
L'installazione di un massetto in cemento-sabbia è la più collaudata e modo affidabile per livellare la superficie. Con il suo aiuto, il pavimento non solo viene livellato, ma conferisce anche la rigidità necessaria, che sarà necessaria per ulteriori lavori. Puoi acquistare una miscela già pronta per organizzare il massetto nei negozi di costruzioni oppure puoi prepararla tu stesso.
Composizione e proporzioni del massetto cemento-sabbia.
La composizione del massetto cemento-sabbia comprende, come suggerisce il nome, cemento, sabbia e acqua. Per plasticità, puoi aggiungere un plastificante. Per un massetto normale viene utilizzata una soluzione di grado M 150 Proporzioni per ottenere il grado richiesto di miscela cemento-sabbia: per 1 sacco di cemento (50 kg) è necessario prelevare 150 kg di sabbia (circa 10 secchi da 10). litri) e circa 25-27 litri di acqua. La quantità di acqua dipende in gran parte dal contenuto di umidità della sabbia. Maggiore è il contenuto di umidità della sabbia, minore è la quantità di acqua necessaria.
Consumo peso e densità del massetto cemento-sabbia.
La densità del massetto cemento-sabbia dipende direttamente dalla scelta dei materiali utilizzati. Si dividono in leggeri e pesanti. Massetto leggero- densità fino a 1400 kg/m3, pesante – oltre 1400 kg/m3. Maggiore è la densità della composizione, maggiore è la forza e la resistenza al gelo. Viene utilizzato qualsiasi tipo di composizione. Il consumo di massetto cemento-sabbia non è difficile da calcolare in base ai dati del produttore (guarda il retro della borsa). Il consumo di massetto in cemento-sabbia è di circa 20 kg per 1 m2, con uno spessore dello strato di 10 mm. In questo caso il peso del massetto cemento-sabbia sarà di circa 15-20 kg. per ogni centimetro di spessore.
Spessore minimo e massimo del massetto cemento-sabbia.
Raccomandato spessore minimo massetto in cemento-sabbia – 30 mm. Se lo spessore minimo del massetto è inferiore, apparirà sicuramente piccole crepe. Lo spessore massimo del massetto cemento-sabbia è solo limitato capacità portante sovrapposizione e aumento dello spreco di materiale. Con uno spessore di 80-100 mm il peso del massetto raggiungerà i 150-200 kg per metro quadrato, il che non è sempre accettabile. Lo spessore ottimale consigliato dagli esperti è 30-50 mm.
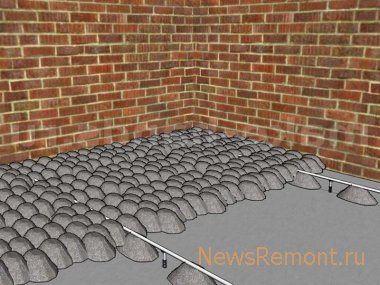
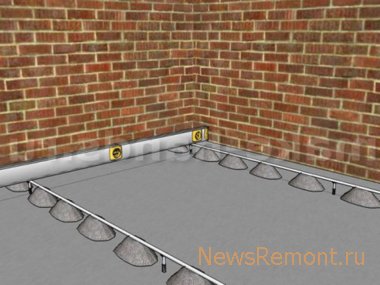
Installazione di massetto in cemento-sabbia.
L'installazione del massetto in cemento-sabbia inizia riempiendo con una pala lo spazio tra i fari precedentemente installati. La posa del massetto cemento-sabbia deve essere eseguita velocemente per evitare che la soluzione indurisca prematuramente. Se il lavoro viene svolto da solo, è necessario compilare una corsia alla volta. Dopo il riempimento, la soluzione solitamente si allunga. Se compaiono piccoli buchi e spazi vuoti, è necessario aggiungere una soluzione lì. Il massetto viene solitamente serrato più volte fino ad ottenere una superficie liscia. Il massetto è pronto. Non resta che aspettare che si asciughi. Durante il processo di essiccazione, per evitare la comparsa di crepe, si consiglia di annaffiarlo una piccola quantità acqua.Il massetto in cemento-sabbia (CSS) è un metodo semplice e di rapida implementazione per livellare i rivestimenti del pavimento. Utilizzando il DSP è possibile livellare pavimenti in pietra e cemento, preparandoli per la posa pavimentazione di finitura. Tra i suoi vantaggi ci sono la durabilità, la resistenza alla deformazione sotto l'influenza di carichi di qualsiasi tipo e il basso costo.
In questo articolo viene discussa la realizzazione di un massetto cemento-sabbia. Imparerai come calcolare i materiali, preparare la malta, installare i fari, riempire e livellare la lastra centrale.
Peso, tempo di stagionatura, tipologie di DSP
L'unico fattore che limita la possibilità di utilizzare il massetto cemento-sabbia è il suo peso elevato. Sì, peso metro quadrato Il CPS con spessore di 1 cm può arrivare fino a 15 kg/m2. Allo stesso tempo, lo spessore minimo del massetto cementizio è di 3 cm, quindi in pratica (se si tiene conto del peso dell'isolante e del rivestimento anteriore del pavimento - laminato o tavola di parquet) 1 m 2 di massetto pesa almeno 50 chilogrammi. Nella maggior parte dei casi, lo spessore del DSP versato è di 5 cm, se si posiziona una piastrella su un massetto di questo tipo, il suo peso sarà di circa 100 kg/m2;
Di conseguenza, l'uso del massetto per livellare i pavimenti del primo piano non è tuttavia limitato edifici a più piani può essere utilizzato solo in ambienti in cui i solai portanti sono progettati per un carico di almeno 300 kg/m2.
Il periodo di asciugatura del massetto cemento-sabbia dipende direttamente dal suo spessore. Pertanto, un DSP di 40 mm di spessore si asciuga entro 7 giorni e con ogni aumento di spessore di 1 cm sono necessari 5 giorni aggiuntivi per acquisire resistenza.
Esistono due modi per livellare il pavimento con un massetto: utilizzare miscela pronta per fibrocemento centrale o preparazione malta sabbia-cemento con le proprie mani. Secondo le disposizioni del GOST n. 28013, le miscele acquistate in negozio sono classificate in due tipologie: secche - miscelate direttamente in cantiere e umide - fornite in una forma pronta per l'uso. Tra le miscele comprovate che hanno un rapporto qualità/prezzo ottimale, evidenziamo composizioni come Knauf OP-135, Ceresit CN-69 e Knauf UBO. Si tratta di miscele secche che vengono vendute in sacchi da 25 kg.
Un'attenzione particolare merita la miscela Knauf-UBO, che contiene granuli di polistirene espanso. Grazie a questo riempitivo, il massetto riceve ulteriori capacità di isolamento termico, che è particolarmente importante quando si livella un pavimento freddo al primo piano di una casa. Il consumo di malta preparata con la miscela Knauf-UBO per 1 m2 di pavimento è di 17,6 kg con uno spessore del massetto di 3 cm. La densità del rivestimento è di 600 kg/m3, la resistenza dopo l'indurimento è di 1 MPa.
Esistono anche composizioni con aggiunta di fibra di fibra, che aumenta la robustezza e la resistenza del massetto alle fessurazioni, che consente di non utilizzare la rete d'acciaio durante il getto. L'utilizzo della fibra DSP consente di risparmiare tempo e denaro rispetto all'installazione di un analogo classico, mentre il costo di tale miscela non è molto diverso dalle miscele per massetti convenzionali.
1.1 Composizione, consumo di materiale
La malta del massetto contiene acqua, sabbia e cemento Portland. È necessario utilizzare cemento per massetto di classe M400, la nomenclatura numerica in questo caso significa che dopo l'indurimento il calcestruzzo potrà sopportare un carico fino a 400 kg/cm2.
Le proporzioni dei componenti nella soluzione sono 4 parti di sabbia e 1 parte di cemento. La quantità di acqua viene determinata in base al peso del cemento aggiunto: 0,5 litri per chilogrammo. La soluzione preparata deve avere una consistenza sufficientemente densa in modo che dopo averla versata non si diffonda quando si cerca di livellare il massetto con una forchetta.
Il consumo medio di cemento per un massetto di 5 cm di spessore è di 15 kg/m2. È possibile determinarne con precisione la quantità eseguendo un calcolo. Presentiamo un algoritmo per tale calcolo utilizzando l'esempio di un pannello centrale in fibra con uno spessore di 4 cm e una superficie di 25 m2:
- Determiniamo il volume del massetto moltiplicandone l'area e lo spessore: 25*0,04 = 1 m3.
- Tenendo conto delle proporzioni di composizione di 4:1, calcoliamo il volume di ciascun componente: ¼ = 0,2 m3.
- Calcoliamo il volume effettivo di 4 parti di sabbia: 4 * 0,2 = 0,8 m 3 e una parte di cemento: 1 * 0,2 = 0,2 m 3.
- Sulla base dei dati di riferimento, determiniamo il peso specifico di 1 m 3 di sabbia, che è 1600 kg, e cemento - 1300 kg.
- Calcoliamo il consumo di materiali per cementare un massetto di determinate dimensioni: cemento: 0,2 * 1300 = 260 kg, sabbia - 0,8 * 1600 = 1280 kg.
Pertanto, il calcolo ha mostrato quanti materiali sarebbero necessari per riempire il massetto. Tuttavia, devono essere acquistati con un margine del 15-20%, poiché durante la preparazione della soluzione il cemento si restringe di volume.
1.2 Cosa è necessario sapere quando si versa il massetto? (video)
2 Tecnologia di riempimento DSP
La preparazione del sottofondo prima della gettata del massetto inizia con la sua pulizia. È necessario picchiettare l'intero pavimento o solaio e rimuovere i pezzi di calcestruzzo sciolti e riempire con malta i fori risultanti; Successivamente, è necessario rivestire la superficie con un primer, che aumenterà l'adesione tra la base e il DSP. È necessario primerizzare in due strati, il secondo viene applicato dopo il tempo necessario affinché il primo strato si asciughi completamente.
È più conveniente contrassegnare il massetto utilizzando livella laser. Il dispositivo viene installato nel punto più alto del pavimento della stanza, i suoi indicatori sono posizionati lungo le pareti della stanza e su di essi vengono fatti appositi segni.
Il prossimo passo è installare i beacon. Queste sono le guide di profilo metallico, lungo il quale verrà livellato il massetto dopo il getto. Esistono due tipi di fari: acciaio convenzionale e malta, consigliamo di utilizzare la prima opzione, poiché richiede meno manodopera e fornisce una migliore precisione di allineamento; La larghezza tra i fari installati deve essere di 20 cm inferiore alla larghezza del cavo utilizzato.
I fari vengono posizionati su una torta di malta; puoi anche usare pezzi di mattoni e schiuma di poliuretano. Il bordo superiore del faro dovrebbe trovarsi lungo la linea del contorno superiore del massetto. Tieni presente che il faro non deve abbassarsi lungo la sua lunghezza, per evitare ciò è necessario utilizzare un numero sufficiente di supporti.
Successivamente, la soluzione viene miscelata. Proporzioni: 1 parte di cemento, 4 parti di sabbia e 0,5 litri di acqua per chilogrammo di cemento. È necessario iniziare a gettare il calcestruzzo dalla parte della stanza più lontana dalla porta: la soluzione viene versata sulla base da un secchio e livellata lungo i fari utilizzando una forchetta. In questo modo vengono coperte superfici di 1-2 m2.
Dopo 12-15 ore dal getto, la superficie del massetto dovrà essere strofinata con una miscela di cemento e sabbia (1 a 1). Questo viene fatto usando una cazzuola speciale o utensili manuali realizzato in polistirene espanso. Durante il processo di macinazione vengono rimosse dalla superficie tutte le irregolarità causate in fase di riempimento. Dopo la stuccatura, il massetto dovrà essere inumidito con rullo bagnato e ricoperto con tela cerata, la bagnatura dovrà essere ripetuta quotidianamente per 7 giorni;
Qualche parola sul rinforzo. Ciò avviene qualora sia necessario compensare i carichi di flessione e vibrazione agenti sul massetto, eventualmente presenti locali di produzione o nel caso di livellamento di una base elastica soggetta a deformazioni - solai a travetti, pannelli termoisolanti. In questo caso, il telaio di rinforzo o la rete di acciaio annegata nel massetto si fa carico del carico, riducendo il rischio di deformazione del calcestruzzo.
Se stai livellando il pavimento in una zona residenziale con un massetto, molto probabilmente non è necessario alcun rinforzo. Se si decide di rinforzare, è meglio utilizzare una rete stradale con una dimensione delle celle di 100 * 100 mm. La rete viene posata su supporti: pezzi di mattoni o torte di cemento in modo che sia sollevata sopra il pavimento della metà dello spessore del massetto e sopra di essa siano posizionati dei fari. Dovrebbe esserci una distanza di 5 mm tra le pareti della stanza e i bordi della rete. Il processo di betonaggio stesso viene eseguito utilizzando la tecnologia standard.